How Does the New Z87.1 – 2010 Eye Safety Standard Impact You?
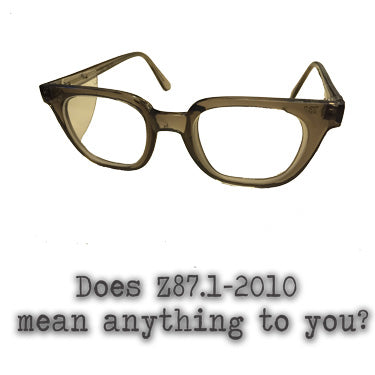
Everyone who wears safety glasses is impacted (no pun intended) by the 2010 ANSI Standard involving eye protection. While the standard is still based on how the product performs, it is now organized by hazard types. These changes add new requirements for testing, rating, and labeling of all safety glasses. So, let’s take a moment to unpack and understand how this relates to the typical employee and employer who currently uses safety glasses.
Gone are the days of the old heavy 1950’s-style safety spectacles with glass lenses. We are in the 21st Century, right? We have seen virtually every style of safety glass used and that is a good thing. It means that style, fit and comfort have all helped promote the use of safety glasses all the while remaining a safe and “approved” piece of PPE (Personal Protection Equipment). Now, the 2010 standard requires us to consider the type of hazard we will be working around and select the appropriate type of protection. Each of these hazard types brings new testing and performance requirements the safety eyewear manufacturer will need to take into consideration. It will also mean that new products will be required to display the appropriate labeling so you the employee/employer will know if the safety eyewear is approved for your hazard! Here are the 4 main Safety Eyewear classifications ANSI wants you to know about.
1. Impact & Coverage
Previously, Safety Eyewear was classified as Basic or High impact but the new standard now simplifies this. Glasses are either rated for impact or they aren’t. So, new glasses that have the Z87+ marking are compliant. Prescription safety eyewear that is compliant will be marked with Z87-2+ markings. These markings affirm that the safety eyewear meets high mass and velocity impact tests as well as lateral coverage protecting the eyes and will be placed on the lens and the frame.
2. Chemical Splash & Dust
New product requirements and test methods have been added for products intended to provide protection against chemical splash, dust, and fine dust. Protectors meeting the requirements will be marked D3, D4, or D5, respectively, on their frames or housings. While we won’t detail each of the different levels D3-5, know that products may satisfy more than one use category and will be marked accordingly.
3. Optical Radiation
Welding applications that expose the worker to Optical Radiation are rated and require different shaded filters to protect them. These levels of protection are based on the intensity of the hazard. For example, welding filters will be marked with a “W” and the required shade for the application will follow after the filter type. So a shade 10 welding filter will be marked W10. In short, Ultraviolet, Infrared, Visible Light, and other types of potential optical radiation are identified and scaled. The manufacturer of the safety eyewear will rate their product performance using these designators and scales.
4. SIZE REQUIREMENTS
The eyewear industry is aware that people of all sizes and shapes will need to wear safety glasses. ANSI has rated products designed for smaller heads with the letter “H”.
So, what is the takeaway here? If you are wearing safety eyewear that has the Z87.1 markings you are in compliance. The Z87.1-2010 standard is in effect and incorporated into the OSHA regulations covering PPE however the regulations allow the 3 latest versions of the standard to still be used. Manufacturers will include new markings as they bring new products to the market. We suggest you begin to look at safety eyewear requirements from the perspective of the potential hazards and become more familiar with the standard. More details about the changes can be found at www.safetyequipment.org. Copies of the standard may be obtained through ANSI at www.ansi.org.
Eye Safety Products & Accessories
Safety Glasses
Lens Cleaning Products
Safety Glasses Accessories
Additional Resources for Eye Safety & Supplies
How Do Safety Glasses Protect Your Eyes?
How To Disinfect Safety Glasses
5 Tips for Workplace Eye Safety
Contributing Expert
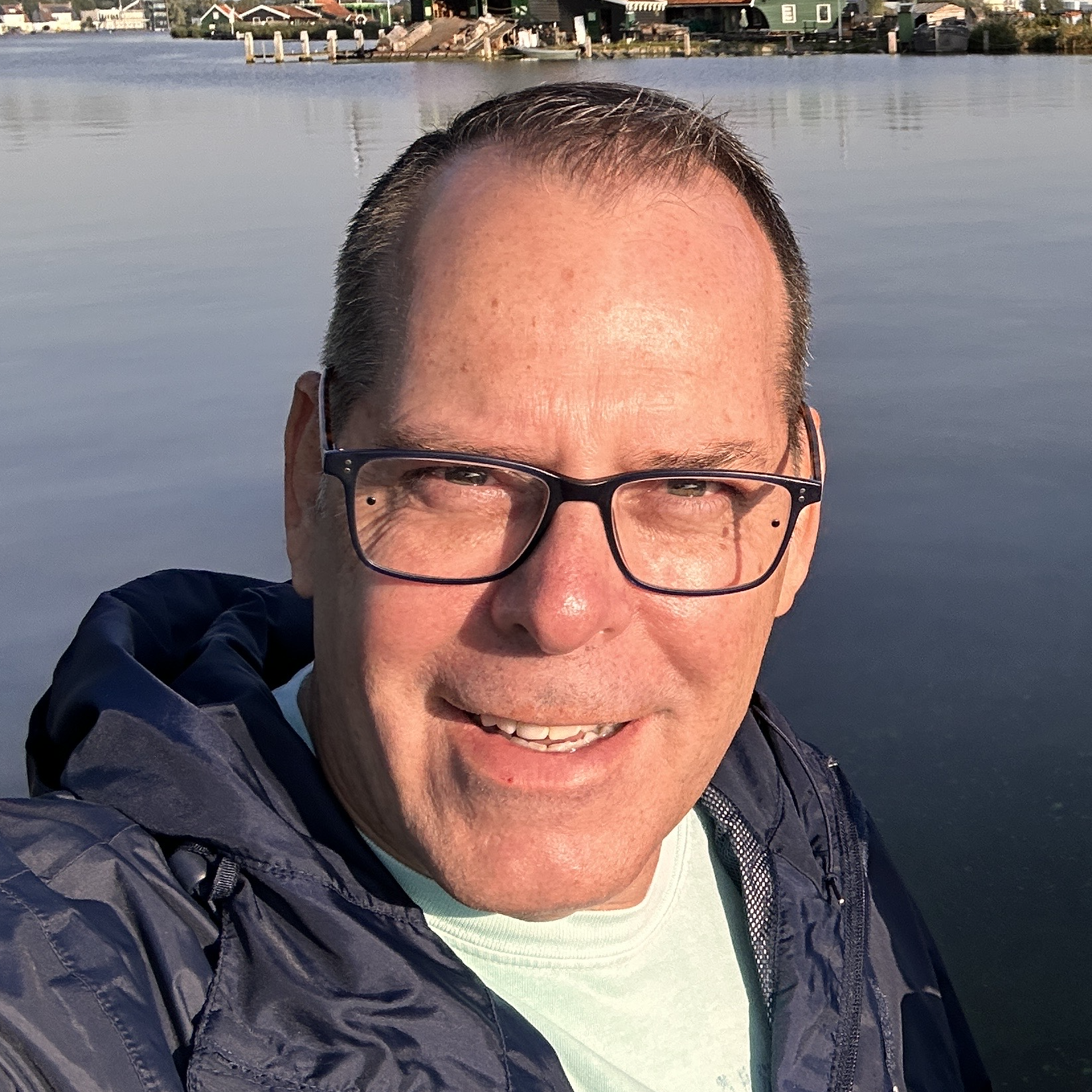
Mike Brinker
Mike Brinker has been working in the first aid industry for over 35 years. He has worked with thousands of businesses,groups, and organizations to provide a healthy and safe work environment. Mike helped create “Make-A-Kit”, the internet's only online first aid kit creation tool. He has also authored many helpful first-aid and safety-related resource articles found at the MFASCO Learning Center.